The processing lines for cold rolled sheets
and strips are endowed with special oiling installations, with the
purpose of protecting the sheets and strips surface against the
environment agents that cause their deterioration during long storage
periods or during maritime transportation.
The existing oiling installations employ a pair of rubberized rollers
in permanent contact with the strip, to which the coating oil is
applied through some oil dosage rollers from a tank that is
periodically refilled with the aid of some pumps form an adjacent tank.
This oiling system has the following deficiencies:

it does not allow the
dosing of the quantity of oil deposited and hence the thickness of oil
film deposited on both sides of the strip

significant losses of
oil and its uncontrolled dispersal along the processing line

the oiling
installation is complicated from the mechanical point of view and
uneconomic in operation
GALFINBAND proposes another principle for
the oiling installation, i.e.
by employing some special spraying nozzles, fed from a pumping
installation.
1. The strip which is to be oiled goes through a closed and sealed
casing, endowed with two ramps (up-down) with spraying nozzles on both
its sides. The oil excess is collected at the lower part of the housing
and evacuated by free falling in the pumping tank. The second new
element is the existence of
|
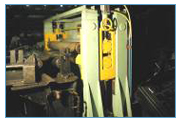 |
a pair of rollers coated with a special polyurethane layer which
homogenizes the thickness of the oil film on the strip. These rollers
are positioned behind the spraying installation. This way, the
installation achieves the dosing of the oil quantity expressed in g/m3,
depending upon the strip speed.
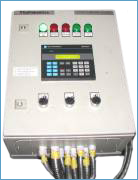 |
2. The oiling degree can be selected from
the control box, which has a
digital display with functional keys: slight oiling, medium oiling or
good oiling.
3. Also, the functioning of the upper part, the lower part or both
parts at the same time can be selected.
4. In order to avoid the depositing of a too large quantity of oil and
therefore to avoid its loss, the installation traces the strip speed,
the position of the leveling roller ' expressed in microns ' (only at
the cut-to-length lines), the oiling times and pause times correlated
with the strip speed and oil temperature. The oiling installation has
an adjustment pump for the oil pressure and temperature (automatically
controlled in order to get the optimal viscosity needed by the spraying
nozzle).
|
5. In the case of cut-to-length lines, the spraying is intermittent
only during the presence of the sheet in the machine. The leveling
rollers for the oil layer thickness are driven by a variable speed
motor for their synchronization with the line speed. In the case of the
slitting lines, the rollers are idle, their rotation being caused by
the strip to be oiled itself.
6. Technical characteristics

Working pressure:
1±3 bar

Oil flow: max 0,8
l/min for a nozzle

Thickness oil layer:
1±10 microns

Optimal working
temperature of oil: 40±50
oC
7. The functions of the automatic guiding and control system:

Functioning regimes:
MANUAL / AUTOMATIC

Process data
acquisition and processing

Sequential control of
the execution elements

Control and adjustment
of the essential parameters

Operator's informing
upon the process progress

Automatic alarming and
protection in case of abnormal situations

Display of the
exception events emerged

Imposing of specific
technological parameters